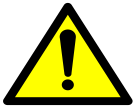
In the early 2000's, VAG began supplying engines with a new direct injection technology known as FSI. Unlike conventional engines of the past, fuel is sprayed directly into the cylinders under extreme pressure resulting in increased power with lower consumption rates and fewer emissions. The technology has spread across VAG's entire lineup of modern gasoline engines and is present in the 4.2L FSI V8.
The engine's fueling system operates to a maximum of 1,973psi (13 bar) of pressure to correctly spray and atomize fuel directly into the engine's cylinders. This is contrast to multi port injection vehicles of the past which typically operated around 40-60 PSI and were driven off of a low pressure fuel pump. To generate these enormous pressures, the 4.2L FSI V8's variable low pressure fuel pump supplies fuel to two cam driven and solenoid fired high pressure fuel pumps which in turn supplies the injectors with fuel.
A dual-lobe cam located on each intake camshaft drive the 4.2L FSI V8's Hitachi high pressure fuel pumps. As engine speed increases, so does each pump's ability to displace a greater volume of fuel per minute. The maximum volume each pump can deliver per revolution on the dual-lobe cam is dictated by the stroke length from each cam lobe's lift and bore diameter of each pump's internal pressurizing cylinder. It's important to understand, despite the name, APR's High Pressure Fuel Pump upgrades are not necessarily designed to increase the engine's fuel rail pressure. The primary goal is to increase the volume of available fuel.
The engine's fueling system is very capable without modification, even at high power levels generated using APR's previously available Stage III TVS130 Supercharger System. However, APR's Stage III+ TVS1740 Supercharger System System is capable of generating significantly more power and requires modification to high pressure fuel pumps to keep up with fueling demands.
Each APR High Pressure Fuel Pump addresses fueling needs and leaves plenty of headroom for safety and further increased power levels in the future. By increasing each pump's internal capacity, the fueling system is capable of displacing a higher volume of fuel per minute at every RPM.
Components
The key to APR's reliability comes in part by use of extremely high grade materials and manufacturing techniques. The most critical components within each HPFP are the enlarged plungers and barrels. Each matched set is created using medical grade precision machining techniques deeply quality controlled all within the USA with dimensional tolerances as tight as .0001" and geometric tolerances as tight as .00009". The plungers and barrels are created from certified and heat-treated bearing-grade stainless steel and undergo a special diamond like coating process for exceptional surfaces hardness and ultra reliable operation. The seals used in each pump are made of a high-performance filled polymer with a high modulus spring to retain the seal forces throughout the life of the product. The cross section of the seal is also of a proprietary design to maintain integrity over many years of use. Finally, to prevent float associated with altering the plungers mass, APR supplies each unit with a properly spec'd spring.
Ultimate reliability of this critical component is not easily created using inferior materials and manufacturing techniques. Across all direct injection markets, the community has come to see time after time, cheaper alternatives were met with sometimes irreversible engine damage. Leaking seals result in gasoline entering the engine's oiling system and seized pistons due to weak tolerances and wear can result in increased wear or destruction of the engine's camshaft and connected components.
- PDP tag:
- Free Shipping*
- Sales:
- On Sale
- PDP tag:
- On Sale